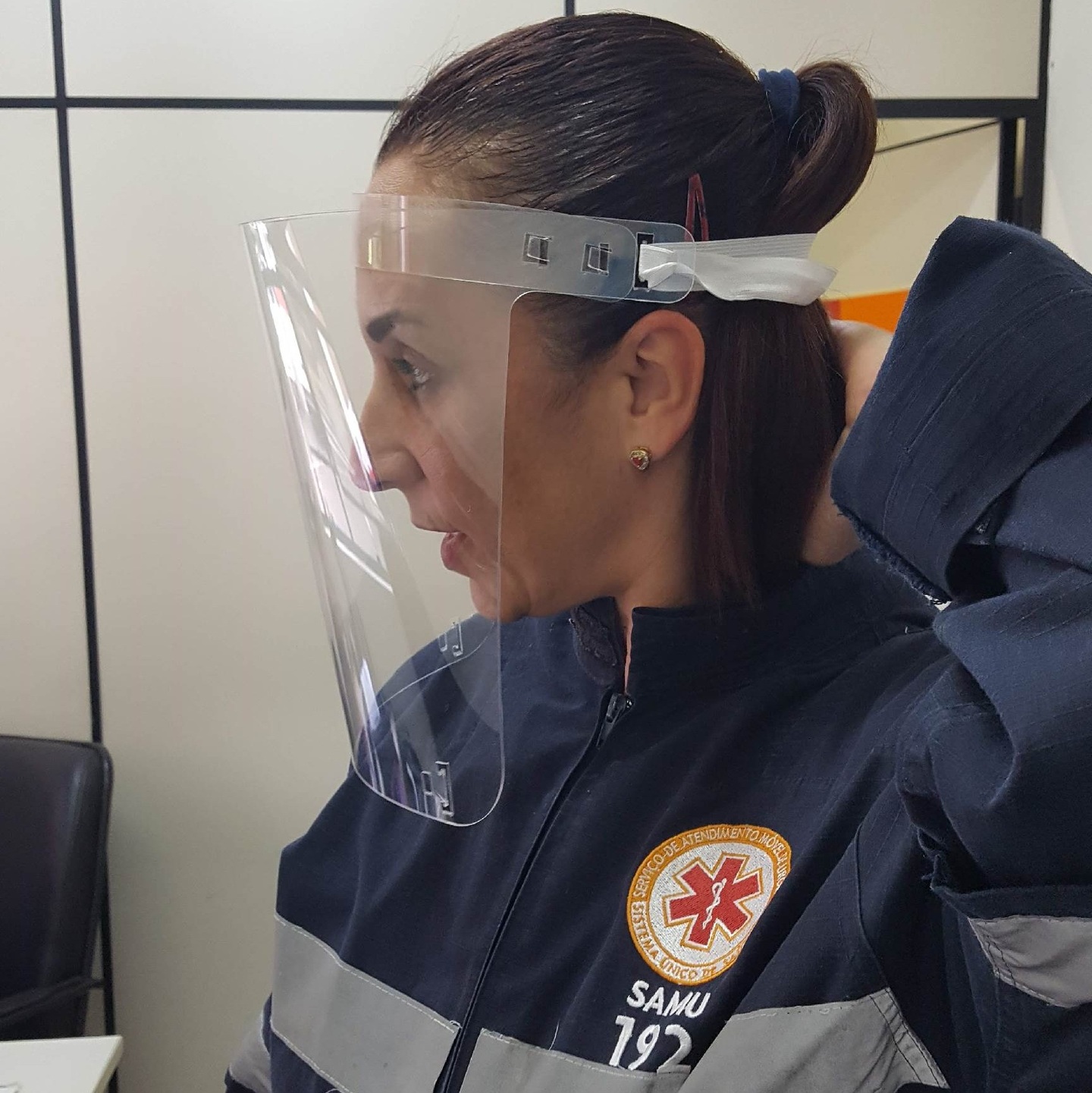
A partir das primeiras notícias sobre o alastramento da COVID-19 na Itália e uso de tecnologias de manufatura aditiva para auxiliar no combate a pandemia, o grupo de pesquisa NPro do DEP UFSCar, coordenado pelo prof. Daniel Braatz e com apoio do prof. Renato Luvizoto (UFTM) e o estudante de graduação da UFSCar Esdras Paravizo, iniciaram uma pesquisa para compreender como a universidade pública junto com a comunidade maker (pessoas que utilizam equipamentos de fabricação digital e adeptas do movimento faça-você-mesmo) poderiam atuar no mesmo sentido.
Com a utilização de impressoras 3D e máquina de corte à laser, foram feitos diversos protótipos de máscaras com proteção facial (faceshields) e após algumas alterações de design de engenharia alguns modelos foram levados até hospitais e serviços de atendimento de saúde para testes e simulações com profissionais da área de saúde. Neste momento o NPro começou a atuar em uma rede colaborativa que inclui o NUMA-EESC-USP (sob coordenação da Prof. Zilda Silveira, juntamente com outros pesquisadores e empresas), um grupo de docentes e técnicos administrativos de diversos departamentos da UFSCar (coordenados pelo prof. Rafael Aroca, diretor da Agência de Inovação) e diversas outras universidades públicas e empresas privadas.
Em paralelo a estas ações, os professores Daniel Braatz, Fábio Molina e Fabiane Lizarelli (docentes do DEP UFSCar) iniciaram um movimento para aumentar a escala de produção de forma a atender a demanda por faceshields dos hospitais, unidades de saúde e outros serviços de atendimento de São Carlos e região. O objetivo era sair da escala possível com uso de impressoras (entre 100 e 200 máscaras por dia, produzidas de forma descentralizada, com diferentes modelos e materiais) para uma escala e padrão industrial (em torno de 200 peças por hora ou 1600 por dia).
Para criar essa rede de colaboração, esse conjunto de professores uniu diferentes empresas e pesquisadores para que fosse possível criar um modelo de faceshield que pudesse ser injetado e que considerasse questões como ergonomia, usabilidade, segurança do trabalho, qualidade, disponibilidade de materiais no mercado, logística, entre outras áreas que são conhecidas da engenharia de produção.
O resultado desta rede é que dois moldes foram produzidos em tempo recorde (menos de 4 dias) na cidade de Birigui graças ao apoio de duas empresas privadas que doaram os materiais e realizaram a usinagem dos moldes (Solis Industria e Comercio de Aquecedor Solar S.A. e Fiveltec Indústria de Metais Ltda.) e do IFSP-Birigui no apoio ao projeto. Um dos moldes ficará em Birigui e o outro está sendo trazido para São Carlos para iniciar a injeção de peças em outra empresa. As primeiras peças injetadas para teste foram produzidas no dia 9 de abril e uma delas pode ser vista na foto abaixo.
O próximo passo desta rede é angariar doações de materiais para a viabilização desta escala de produção e posterior fornecimento deste equipamento complementar de proteção para os profissionais de saúde de diversas cidades do estado de São Paulo. Atualmente, com o uso das impressoras 3D e máquina de corte à laser, já foi possível atender parcialmente a Santa Casa, Hospital Universitário e SAMU de São Carlos e entidades de Araraquara, Piracicaba, Sertãozinho, Matão, Porto Ferreira, entre outras.
Para saber como você pode colaborar entre em contato através do e-mail doecovid@ufscar.br ou acesse a página de doações http://www.fai.ufscar.br/doacao?projeto=covid19-13387